Verskeie probleme waaraan aandag gegee moet word by die giet van natriumsilikaatsand
1 Wat is die faktore wat die 'veroudering' van waterglas beïnvloed? Hoe om die 'veroudering' van waterglas uit te skakel?
Die varsgemaakte waterglas is 'n ware oplossing. Tydens die opbergingsproses ondergaan die silikensuur in die waterglas egter kondensasiepolymerisasie, wat geleidelik uit die ware oplossing polykondenseer tot 'n makromolekulêre silikensuuroplossing en uiteindelik 'n silikensuurgel word. Daarom is waterglas eintlik 'n heterogene mengsel wat bestaan uit polisiliensuur met verskillende polimerisasiegraderings, wat maklik beïnvloed word deur die modulus, konsentrasie, temperatuur, elektrolietinhoud en bergingstyd.
Tydens opberging ondergaan die waterglasmolekules kondensasiepolymerisasie om 'n gel te vorm, en die bindingssterkte daarvan neem geleidelik af met die verlenging van die bergingstyd. Hierdie verskynsel word 'veroudering' van waterglas genoem.
Die verskynsel "veroudering" kan verklaar word deur die volgende twee stelle toetsdata: waterglas met hoë modulus (M = 2.89, ρ = 1.44g/cm3) na 20, 60, 120, 180, 240 dae stoor, die CO2 verhard waterglas word geblaas Die droë treksterkte van sand val ooreenstemmend met 9.9%, 14%, 23.5%, 36.8%en 40%; lae modulus natriumsilikaat (M = 2.44, ρ = 1.41g/cm3) word vir 7, 30, 60 en 90 dae gestoor nadat dit gedroog is. Die treksterkte het onderskeidelik met 4.5%, 5%, 7.3% en 11% afgeneem.
Die bergingstyd van waterglas het min invloed op die aanvanklike sterkte van ester-geharde waterglas selfverhardende sand, maar dit het 'n beduidende uitwerking op die latere sterkte. Volgens metings word dit met ongeveer 60% verminder vir waterglas met hoë modulus en 15-20% vir waterglas met 'n lae modulus. . Die oorblywende sterkte neem ook af met die verlenging van die bergingstyd.
Tydens die berging van waterglas gaan die polykondensasie en depolymerisasie van polisiliensuur gelyktydig voort, die molekulêre gewig is buite verhouding, en uiteindelik ontstaan 'n multi-verspreide stelsel waarin monoortosiliensuur en kolloïdale deeltjies saamleef. Dit wil sê, tydens die verouderingsproses van waterglas, is die polimerisasiegraad van kiselsuur onproportioneel, en die inhoud van monoortosiliensuur en hoë polisiliensuur neem toe met die verlenging van die bergingstyd. As gevolg van kondensasiepolymerisasie en depolymerisasie -reaksie van waterglas tydens opberging, word die bindingssterkte verminder, dit wil sê dat die verskynsel van "veroudering" voorkom.
Die belangrikste faktore wat die 'veroudering' van waterglas beïnvloed, is: bergingstyd, modulus en konsentrasie van waterglas. Hoe langer die bergingstyd, hoe hoër die modulus en hoe groter die konsentrasie, hoe ernstiger word die "veroudering".
Die reeds bestaande waterglas kan op verskillende maniere aangepas word om 'veroudering' uit te skakel en die waterglas weer in die toestand van varswaterglas te herstel:
1. Fisiese verandering
Die veroudering van waterglas is 'n spontane proses wat stadig energie vrystel. Die fisiese verandering van 'verouderde' waterglas is om magnetiese veld, ultraklank, hoë frekwensie of verwarming te gebruik om energie aan die waterglasstelsel te verskaf en die hoë polimerisasie van polisilikaatgom te bevorder. Die deeltjies herpolymeriseer en bevorder die homogenisering van die molekulêre gewig van polisiliensuur, waardeur die verouderingsverskynsel, wat die meganisme van fisiese modifikasie is, uitgeskakel word. Byvoorbeeld, na behandeling met 'n magnetiese veld word die sterkte van natriumsilikaat sand met 20-30%verhoog, die hoeveelheid natriumsilikaat wat bygevoeg word, word verminder met 30-40%, CO2 word bespaar, die opvoubaarheid word verbeter, en daar is goeie ekonomiese voordele.
Die nadeel van fisiese modifikasie is dat dit nie duursaam is nie, en dat die bindingssterkte afneem wanneer dit na behandeling gestoor word, dus dit is geskik vir gebruik so gou as moontlik na behandeling in die gieterij. Veral vir waterglas met M> 2.6, is die konsentrasie kielsuurmolekules groot, en na fisiese aanpassing en depolymerisasie sal dit relatief vinnig polikondenseer. Dit is die beste om dit onmiddellik na behandeling te gebruik.
2. Chemiese modifikasie
Chemiese modifikasie is om 'n klein hoeveelheid verbindings by die waterglas te voeg; hierdie verbindings bevat almal karboksiel, amied, karboniel, hidroksiel, eter, amino en ander polêre groepe, wat deur silikoonzuurmolekules of kolloïdale deeltjies geabsorbeer word deur waterstofbindings of statiese elektrisiteit. Oppervlak, verander die potensiële energie- en oplosvermoë van die oppervlak, verbeter die stabiliteit van polisiliensuur en voorkom dat 'veroudering' voortgaan.
Byvoorbeeld, die toevoeging van poliakrylamied, gemodifiseerde stysel, polifosfaat, ens. By die waterglas kan beter resultate behaal.
Om organiese materiaal in gewone waterglas of selfs aangepaste waterglas op te neem, kan 'n verskeidenheid funksies speel, soos: die verandering van die viskose vloei -eienskappe van waterglas; verbetering van die modelprestasie van waterglasmengsels; die verhoging van die bindingssterkte om die waterglas absoluut by te voeg. Die hoeveelheid word verminder; die plastisiteit van die kielsuurgel word verbeter; die oorblywende sterkte word verminder, sodat die waterglas sand meer geskik is vir gietyster en nie-ysterlegerings.
3. Fisies-chemiese modifikasie
Fisiese modifikasie is geskik vir 'verouderde' waterglas, en dit kan onmiddellik na die wysiging gebruik word. Chemiese modifikasie is geskik vir die verwerking van vars waterglas en die aangepaste waterglas kan lank gestoor word. Die kombinasie van fisiese modifikasie en chemiese modifikasie kan die waterglas 'n blywende modifikasie -effek hê. Byvoorbeeld, die toevoeging van poliakrylamied by die outoklaaf om die "veroudering" waterglas te verander, het 'n goeie effek. Onder hulle word die druk en die druk van die outoklaaf gebruik. Roer is 'n fisiese verandering, en die toevoeging van poliakrylamied is 'n chemiese verandering.
2 Hoe om te verhoed dat CO2 verhard natriumsilikaat sandvorm (kern) oppervlakkryt blaas?
Nadat soda natriumsilikaat sand met CO2 verhard en 'n rukkie gelos word, verskyn daar soms 'n stof soos ryp op die oppervlak van die onderste vorm (kern), wat die oppervlaksterkte van die plek ernstig sal verminder en maklik sand kan produseer wasfoute tydens giet. Volgens analise is die hoofkomponent van hierdie wit stof NaHCO3, wat veroorsaak kan word deur oormatige vog of CO2 in die natriumsilikaat sand. Die reaksie is soos volg:
Na2CO3+H2O → NaHCO3+NaOH
Na2O+2CO2+H2O→2NaHCO3
NaHCO3 migreer maklik na buite met vog, wat poeieragtige ryp op die oppervlak van die vorm en kern veroorsaak.
Die oplossing is soos volg:
1. Beheer die voginhoud van die natriumsilikaat sand om nie te hoog te wees nie (veral in die reënseisoen en winter).
2. Die tyd om CO2 te blaas, moet nie te lank wees nie.
3. Die geharde vorm en kern moet nie lank geplaas word nie en moet betyds gegiet en gegooi word.
4. Om ongeveer 1% (massa -fraksie) van die stroop met 'n digtheid van 1.3 g/cm3 by die natriumsilikaat sand te voeg, kan effektief verhoed dat die oppervlak poeier.
3 Hoe kan ek die weerstand teen vogopname van die waterglas sandvorm (kern) verbeter?
Die kern van soda -glasglas -sand wat verhard word deur CO2 of verwarmingsmetodes, word in die nat kleivorm saamgevoeg. As dit nie betyds gegiet word nie, sal die sterkte van die sandkern skerp afneem, en kan dit nie net kruip of selfs ineenstort nie; dit word in 'n vogtige omgewing geberg. Die sterkte van die sandkern word ook aansienlik verminder. Tabel 1 toon die sterktewaarde van die CO2 geharde natriumwater glas sandkern wanneer dit 97 uur in 'n omgewing met 'n relatiewe humiditeit van 24% geplaas word. Die rede vir die verlies aan sterkte wanneer dit in 'n vogtige omgewing geberg word, is te danke aan die herhidrasie van natriumwaterglas. Die Na+ en OH— in die natriumsilikaatbindmiddelmatriks absorbeer vog en erodeer die matriks, en breek uiteindelik die silikon-suurstofbinding Si-O-Si, wat 'n beduidende afname in die bindingssterkte van die natriumsilikaat sand tot gevolg het.
1. Litium waterglas word by natriumwaterglas gevoeg, of Li2CO3, CaCO3, ZnCO3 en ander anorganiese bymiddels word by natriumwaterglas gevoeg, omdat relatief onoplosbare karbonate en silikate gevorm kan word en vrye natriumione verminder kan word. opnameweerstand van die natriumwaterglasbinder kan verbeter word.
2. Voeg 'n klein hoeveelheid organiese materiaal of organiese materiaal met oppervlakaktiewe funksie by die natriumwaterglas. As die bindmiddel verhard word, kan die hidrofiliese Na+ en OH-ione in die natriumwaterglasgel deur organiese hidrofobiese groepe vervang word, of in kombinasie met mekaar kan die blootgestelde organiese hidrofobiese basis vogabsorpsie verbeter.
3. Verbeter die modulus van waterglas, omdat die vogweerstand van waterglas met 'n hoë modulus sterker is as die van waterglas met 'n lae modulus.
4. Voeg styselhidrolisaat by natriumsilikaat sand. 'N Beter metode is om styselhidrolisaat te gebruik om natriumwaterglas te verander.
4 Wat is die kenmerke van die CO2-blaas van geharde waterglas-alkaliese fenoliese harssand saamgestelde proses?
Om die kwaliteit van staalgietstukke te verbeter, moet sommige klein en mediumgrootte ondernemings die harssandproses dringend gebruik. As gevolg van die beperkte ekonomiese kapasiteit, kan hulle nie harssandherwinningstoerusting aanskaf nie, en die ou sand kan nie herwin word nie, wat lei tot hoë produksiekoste. Om 'n effektiewe manier te vind om die kwaliteit van gietstukke te verbeter sonder om die koste te veel te verhoog, kan die proseskenmerke van CO2 waai geharde natriumsilikaat sand en CO2 waai geharde alkaliese fenoliese harssand gekombineer word, en CO2 waai geharde natriumsilikaat - alkalies fenoliese hars kan gebruik word. Die harssandverbindingsproses gebruik alkaliese fenoliese harssand as die oppervlaktesand en waterglas sand as die agterste sand, terwyl CO2 waai vir verharding.
Die fenolhars wat in CO2-alkaliese fenolharsand gebruik word, word vervaardig deur polikondensasie van fenol en formaldehied onder die werking van 'n sterk alkaliese katalisator en die toevoeging van 'n koppelingsmiddel. Die PH-waarde daarvan is ≥13, en die viskositeit daarvan is ≤500mPa • s. Die hoeveelheid fenolhars wat by die sand gevoeg word, is 3% tot 4% (massa -fraksie). As die CO2 -vloeitempo 0.8 ~ 1.0m3/h is, is die beste waai tyd 30 ~ 60s; as die blasertyd te kort is, sal die verhardingssterkte van die sandkern laag wees; As die waai tyd te lank is, sal die sterkte van die sandkern nie toeneem nie, en dit is vermorste gas.
CO2 — Alkaliese fenoliese harssand bevat geen skadelike elemente soos N, P, S, ensovoorts nie, sodat gietdefekte soos porieë, mikrokrake, ens. Wat deur hierdie elemente veroorsaak word, uitgeskakel word; skadelike gasse soos H2S en SO2 word nie vrygestel tydens giet nie, wat voordelig is vir die beskerming van die omgewing; Goeie opvoubaarheid, maklik om skoon te maak; hoë dimensionele akkuraatheid; hoë produksiedoeltreffendheid.
Die saamgestelde proses met CO2-blaas van verhard water, glas-alkaliese fenolhars sand, kan wyd gebruik word in staalgietstukke, ystergietstukke, koperlegerings en ligte legerings.
Die saamgestelde proses is 'n eenvoudige en maklike proses. Die proses is soos volg: meng eerstens harssand en natriumsilikaat sand afsonderlik en sit dit dan in twee emmers; voeg dan die gemengde harssand as oppervlaktesand in die sandkas en skiet, die dikte van die oppervlak sandlaag is oor die algemeen 30-50mm; dan word waterglas sand bygevoeg om die agterste sand vol en kompak te maak; uiteindelik word CO2 -gas in die vorm geblaas om te verhard.
Die deursnee van die blaasbuis is oor die algemeen 25 mm, en die verhardingsbereik is ongeveer 6 keer die deursnee van die blaasbuis.
Die waai tyd hang af van die grootte, vorm, gasvloei en oppervlakte van die uitlaatprop van die sandvorm (kern). Oor die algemeen word die blaastyd binne 15 ~ 40s beheer.
Nadat u die harde sandvorm (kern) geblaas het, kan die vorm geneem word. Die sterkte van die sandvorm (kern) styg vinnig. Verf die verf binne 'n halfuur nadat u die vorm geneem het, en maak die boks toe om na 4 uur te gooi.
Die saamgestelde proses is veral geskik vir staalgietaanlegte wat nie harssandherstelapparatuur het nie en gietstukke van hoë gehalte moet vervaardig. Die proses is eenvoudig en maklik om te beheer, en die kwaliteit van die vervaardigde gietstukke is gelykstaande aan dié van ander harssandgietstukke.
CO2 blaas geharde natriumsilikaat sand kan ook saamgestel word met CO2 waai geharde natrium poliakrylaat hars sand vir die vervaardiging van verskillende gietstukke van hoë gehalte.
5 Wat is die voor- en nadele van die CO2-organiese ester saamgestelde geharde natriumsilikaat sandproses?
Die afgelope paar jaar het die CO2-organiese ester-saamgestelde geharde natriumsilikaat sandproses 'n neiging om aansoeke uit te brei. Die proses is soos volg: voeg 'n sekere hoeveelheid organiese ester by tydens sandmenging (gewoonlik die helfte van die normale hoeveelheid of 4 ~ 6% van die gewig van waterglas); nadat die modellering voltooi is, blaas CO2 om te verhard tot die vormvrystelling (drukweerstand is oor die algemeen nodig) Die sterkte is ongeveer 0.5MPa); na ontvouing bly die organiese ester verhard, en die sterkte van die gietsand styg vinniger; nadat die CO2 geblaas en 3 ~ 6 uur geplaas is, kan die sandvorm gekombineer en gegooi word.
Die verhardingsmeganisme is:
As die waterglas sand CO2 waai, onder die werking van die gasdrukverskil en die konsentrasieverskil, sal die CO2 -gas in alle rigtings van die vorms probeer vloei. Nadat die CO2 -gas die waterglas raak, reageer dit onmiddellik daarmee om 'n gel te vorm. As gevolg van die diffusie -effek, is die reaksie altyd van buite na binne, en die buitenste laag vorm eers 'n gelfilm, wat verhoed dat die CO2 -gas en die waterglas reageer. Daarom, binne 'n kort tyd, maak nie saak watter metode om CO2 -gas te beheer nie, dit is onmoontlik om dit met alle waterglas te laat reageer. Volgens ontleding is die waterglas wat met CO2 -gas reageer ongeveer 65%wanneer die gietsand die beste blaassterkte bereik. Dit beteken dat die waterglas nie sy bindingseffek ten volle uitoefen nie, en ten minste 35% van die waterglas reageer nie. Die organiese esterverharder kan 'n eenvormige mengsel met die bindmiddel vorm, en kan die bindende effek van die bindmiddel volledig speel. Alle dele van die kernsand bou teen dieselfde snelheid sterkte op.
Deur die hoeveelheid waterglas wat bygevoeg word, te verhoog, word die finale sterkte van die sandvorm verhoog, maar die oorblywende sterkte daarvan sal ook toeneem, wat dit moeilik maak om die sand skoon te maak. As die bygevoegde hoeveelheid waterglas te klein is, is die eindsterkte te klein en kan dit nie aan die vereistes vir gebruik voldoen nie. In die werklike produksie word die hoeveelheid waterglas wat bygevoeg word oor die algemeen op ongeveer 4%beheer.
As u organiese ester alleen gebruik om te verhard, is die algemene hoeveelheid organiese ester wat bygevoeg is 8-15% van die hoeveelheid waterglas. By die gebruik van saamgestelde verharding word geraam dat ongeveer die helfte van die waterglas verhard is wanneer CO2 geblaas word, en ongeveer die helfte van die waterglas het nog nie verhard nie. Daarom is dit meer gepas dat die hoeveelheid organiese esters 4 tot 6% van die hoeveelheid waterglas uitmaak.
Die saamgestelde verhardingsmetode kan die dubbele voordele van CO2 -verharding en organiese ester -verharding ten volle benut, en kan die hechtingseffek van waterglas ten volle uitoefen om vinnige verhardingsnelheid, vroeë vormvrystelling, hoë sterkte, goeie opvoubaarheid en lae koste te bereik. Omvattende effek.
Die CO2-organiese ester-saamgestelde verhardingsproses moet egter 0.5 tot 1% meer waterglas byvoeg as die eenvoudige metode om die organiese ester te verhard, wat die moeilikheid van die herlewing van die gebruikte waterglas sand verhoog.
6 Waarom is dit maklik om taai sand te produseer as die natriumsilikaat sandproses gebruik word om yster gietstukke te vervaardig? Hoe om dit te voorkom?
As die sandvorm (kern) van natriumsilikaat sand gebruik word vir die giet van yster, word dikwels ernstige klewerige sand geproduseer, wat die toepassing daarvan in die vervaardiging van gietyster beperk.
Die Na2O, SiO2 in die natriumsilikaat sand en die ysteroksied wat deur die vloeibare metaal tydens giet gegiet word, vorm laagsmeltende silikaat. Soos vroeër genoem, as hierdie verbinding meer smeltbare amorfe glas bevat, is die bindingskrag tussen hierdie glaslaag en die oppervlak van die gietstuk baie klein en is die krimpkoëffisiënt anders as die van die metaal. Groot spanning kan maklik van die oppervlak van die gietstuk verwyder word sonder dat sand vassteek. As die verbinding wat op die gietoppervlak gevorm word, 'n hoë inhoud van SiO2 en 'n lae FeO, MnO, ens. Bevat, het die gestolde struktuur basies 'n kristallyne struktuur wat stewig gekombineer word met die giet, wat tot klewerige sand kan lei .
As die natriumsilikaat sand gebruik word vir die vervaardiging van yster giet, vanweë die lae giet temperatuur en hoë koolstof inhoud van yster giet, word yster en mangaan nie maklik geoksideer nie, en die gevolglike klewerige sand laag het 'n kristallyne struktuur, en dit is moeilik om 'n geskikte laag tussen die yster gietstukke en die klewerige sandlaag te vestig. Die dikte van die ysteroksiedlaag verskil van die harssand tussen die gietstuk en die klewerige sandlaag, wat 'n helder koolstoffilm deur harspirolise kan produseer by die vervaardiging van yster giet, sodat die taai sandlaag nie maklik verwyder kan word nie.
Om te verhoed dat die produksie van sodawater glas sand uit die vervaardiging van yster giet, kan geskikte bedekkings gebruik word. Soos verf op waterbasis, moet die oppervlak gedroog word nadat dit geverf is, sodat die vinnig droë verf op alkohol gebaseer is.
Oor die algemeen kan yster gietstukke ook 'n gepaste hoeveelheid steenkoolpoeier (soos 3% tot 6%) (massa fraksie) by die natriumsilikaat sand voeg, sodat die pirolise van die steenkool poeier tussen die giet en die sand laag kan produseer 'n helder koolstoffilm. Dit word nie deur metale en hul oksiede benat nie, sodat die klewerige sandlaag maklik van die gietstof afgeskil kan word.
7 Word verwag dat natriumsilikaat sand omgewingsvriendelik vorms word sonder afval van sand?
Waterglas is kleurloos, reukloos en nie-giftig. Dit sal nie ernstige probleme veroorsaak as dit die vel en klere raak en met water spoel nie, maar dit moet vermy word om in die oë te spat. Waterglas bevat geen irriterende of skadelike gasse tydens sandmenging, modellering, verharding en giet nie, en daar is geen swart- en suurbesoedeling nie. As die proses egter onbehoorlik is en te veel natriumsilikaat bygevoeg word, is die ineenstorting van die natriumsilikaat sand nie goed nie, en die stof vlieg tydens sandskoonmaak, wat ook besoedeling kan veroorsaak. Terselfdertyd is dit moeilik om ou sand te herstel, en die afvoer van afval sand veroorsaak alkaliese besoedeling in die omgewing.
As hierdie twee probleme oorkom kan word, kan natriumsilikaat sand omgewingsvriendelike gietvorm word, sonder dat sand afval.
Die fundamentele maatreël om hierdie twee probleme op te los, is om die hoeveelheid waterglas wat bygevoeg word tot minder as 2%te verminder, wat basies die sand kan afskud. As die hoeveelheid waterglas wat bygevoeg word, verminder word, word die oorblywende Na2O in die ou sand ook verminder. Deur 'n betreklik eenvoudige metode van droë regenerasie te gebruik, is dit moontlik om die oorblywende Na2O in die sirkulerende sand onder 0.25%te hou. Hierdie herwinde sand kan voldoen aan die toepassingsvereistes van enkelvormige sand vir klein en mediumgrootte staalgietstukke. Selfs as die ou natriumsilikaat sand nie die duur en ingewikkelde nat metode gebruik om te regenereer nie, maar die relatief eenvoudige en goedkoop droë metode word gebruik, kan dit volledig herwin word, basies word geen afval sand gestort nie en die verhouding van sand tot yster Dit kan verminder word tot minder as 1: 1.
8 Hoe kan ek natriumsilikaat sand effektief regenereer?
As die oorblywende Na2O in die ou natriumsilikaat sand te hoog is, sal die vorms na die byvoeging van die natriumsilikaat nie genoeg bruikbare tyd hê nie, en die ophoping van te veel Na2O sal die vuurvuurheid van die kwarts sand verswak. Daarom moet die oorblywende Na2O soveel as moontlik verwyder word wanneer die gebruikte natriumsilikaat sand regenereer word.
Hou die bron en adres van hierdie artikel vir herdruk:Verskeie probleme waaraan aandag gegee moet word by die giet van natriumsilikaatsand
Minghe Die Casting Company is toegewyd aan die vervaardiging en lewer kwaliteit en hoë werkverrigting gietonderdele (metaal gietgietonderdele sluit hoofsaaklik in Dun-muur giet,Warm kamer Die beslissende,Die Casting van die koue kamer), Ronde Diens (Die Casting Service,CNC-bewerking,Mould Making, Oppervlaktebehandeling). Enige persoonlike aluminium gietstuk, magnesium of Zamak / sink gietstuk en ander gietwerk vereistes is welkom om ons te kontak.
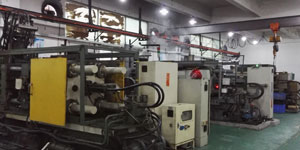
Onder die beheer van ISO9001 en TS 16949, word alle prosesse uitgevoer deur honderde gevorderde gietmasjiene, 5-as-masjiene en ander fasiliteite, wat wissel van blasters tot Ultra Sonic-wasmasjiene.Minghe het nie net gevorderde toerusting nie, maar het ook professionele span ervare ingenieurs, operateurs en inspekteurs om die ontwerp van die kliënt te bewaarheid.
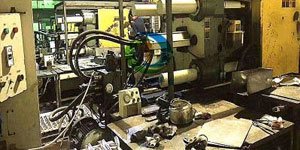
Kontrakvervaardiger van gietstukke. Die vermoëns sluit in gietstukke van aluminium met koue kamer vanaf 0.15 pond. tot 6 lbs., vinnige verandering opgestel, en bewerking. Dienste met toegevoegde waarde sluit in poleer, vibreer, ontbrand, skietblaas, verf, platering, bekleding, montering en gereedskap. Materiaal waarmee gewerk word, bevat legerings soos 360, 380, 383 en 413.
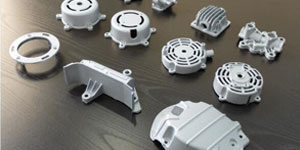
Hulp vir die ontwerp van sinkstukke en gelyktydige ingenieursdienste. Custom vervaardiger van presisie sink giet. Miniatuurgietstukke, gietstukke vir hoë druk, gietstukke vir meervoudige skyfies, konvensionele gietstukke, gietstukke en onafhanklike gietstukke en holtesegelde gietstukke kan vervaardig word. Gietstukke kan in lengtes en breedtes tot 24 duim vervaardig word. +/- 0.0005 duim toleransie.
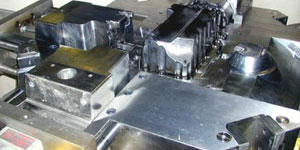
ISO 9001: 2015-gesertifiseerde vervaardiger van gegote magnesium, die vermoëns sluit in hoëdruk magnesiumgietstuk tot 200 ton warmkamer en 3000 ton koue kamer, gereedskapontwerp, poleer, vorm, bewerking, poeier- en vloeibare verf, volledige QA met CMM-vermoëns , montering, verpakking en aflewering.
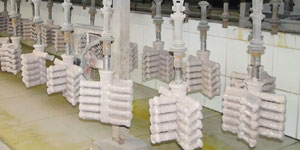
ITAF16949 gesertifiseer. Bykomende rolverdeling sluit in belegging giet,sand giet,Swaartekrag giet, Verlore skuim giet,Sentrifugale giet,Vakuum giet,Permanente gietvormVermogens sluit in EDI, ingenieurshulp, soliede modellering en sekondêre verwerking.
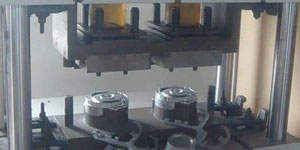
Rolverdelsnywerhede Onderdele Gevallestudies vir: motors, fietse, vliegtuie, musiekinstrumente, watervaartuie, optiese toestelle, sensors, modelle, elektroniese toestelle, omhulsels, horlosies, masjinerie, enjins, meubels, juwele, jigs, telekommunikasie, beligting, mediese toestelle, fotografiese toestelle, Robotte, beeldhouwerke, klanktoerusting, sporttoerusting, gereedskap, speelgoed en meer.
Wat kan ons u help om volgende te doen?
∇ Gaan na die tuisblad vir Die Casting China
→GietonderdeleVind uit wat ons gedoen het.
→ Gesamentlike wenke oor Die Casting Dienste
By Minghe Die Casting vervaardiger | Kategorieë: Nuttige artikels |materiaal Tags: Aluminium giet, Sink giet, Magnesium giet, Titaan giet, Roesvrye staal giet, Koper giet,Brons giet,Rolverdeling-video,Maatskappygeskiedenis,Aluminium gietstuk Kommentaar af